Why preventative maintenance plays an important part in system efficiency
Climalife UK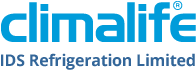
UK Head of Sales, Dave Richards discusses...
With today’s buzzword being energy efficiency due to the rising energy costs, there are also signs that our industry is starting to consider lifetime ownership costs, which includes the, often overlooked, cost of running the equipment in favour of only considering the initial capital expenditure. With this in mind, there are some very simple good practices for existing equipment that can save a lot of money in the long run. For example, money spent on a reliable service and maintenance contract is more than recouped by the energy savings from a clean and cared for system.
Regular servicing and maintenance are essential
One of the basics of servicing is a regular routine oil test, much in the same way that a car’s moving parts benefit from an oil in good condition, so do those in a refrigeration system.
When I first entered this industry, one of the first challenges I had was talking to a successful multi-store fast food franchisee, who had never had his equipment serviced. He happened to drive a smart Jaguar car and I asked him if he had it serviced every year to which he replied ‘of course I do’ seemingly shocked that I had even asked this question. I then asked why he didn’t treat his refrigeration equipment in the same way, which did make him think and after some discussion about prolonging the equipment life and saving him money on his electricity bills, he realised the potential benefits of a service and maintenance contract.
The use of a good quality lubricant in a refrigeration system is imperative to its successful operation and optimum performance. Oil keeps the parts moving, controls wear, reduces friction, absorbs and dissipates heat, as well as sealing and protecting systems from corrosion.
Regular oil testing can help prolong the life of equipment and keep the system operating correctly, playing its part in ensuring the energy efficiency of the system is maintained.
Failure to keep the system in good condition will lead to changes in the oil properties and can lead to an increase in energy consumption, greater wear, and reduced compressor life. If the oil has become contaminated or degraded then the source of the contamination or the reason for the degradation should be found and corrected before a new oil charge is used.
Another good practice is to include an oil change when retrofitting the refrigerant, as the recovered refrigerant will contain some of the oil at the very least it will need to be topped up, so it makes good sense to make a little extra effort and perform an oil change whilst the system is empty.
The choice of oil will depend on the refrigerant, compressor type and design temperatures. Compressor manufacturers will specify which oil and viscosity to use; usually approving specific brands to suit the application and installation but Climalife can also make a recommendation based on the system requirements.
Oil is defined by several key properties:
- The viscosity of oil defines its operating capability at high or low temperatures and its ability to reduce friction within a system and minimise wear and tear.
- Miscibility with the refrigerant so that it returns to the compressor and does not get stuck in the evaporators, impacting the cooling capacity.
All these properties can have an influence over oil return to the compressor; therefore, it is critical that high quality and fit for purpose oil is always used.
Today’s commonly used types of oils can be defined as below:
Hydro Treated Mineral oils (HTMO): Refrigeration equipment using ammonia often requires a specific type of oil to ensure correct operation.
Mineral oils: Mixtures of virtually wax-free hydrocarbons used for the lubrication of refrigeration compressors, selected for their excellent fluidity at low temperatures. This kind of lubricant was particularly suited for use with CFC, HCFC refrigerants and is still used with ammonia.
Alkyl benzene oils: Have enhanced thermal and chemical stability and superior miscibility with hydrochlorofluorocarbons (HCFCs) allowing use at low temperatures. Alkyl benzene oils are not generally recommended for use with HFCs. They are compatible with all traditional mineral oils which they can replace where the system malfunctions with the original lubricant, but it should be noted any mixture of oils may detract from the performance properties of the oil. Very low pour and floc points help to prevent harmful wax precipitation that can block expansion valves and heat transfer surfaces.
Polyol ester synthetic oils (POE): Are the most common type of synthetic oil that can be used with HFC refrigerants and are intended for use in all refrigeration and air conditioning applications.
Poly alkylene glycol oils (PAG): Have a high viscosity index and thermal stability. PAG oils have a benefit in that they can lock in moisture to prevent it being an issue in a refrigeration system. They are extremely stable within the harsh environments of R-744 systems. PAG based lubricants are suitable for use with most commonly used refrigerants including ammonia and carbon dioxide.
Poly-alpha-olefin oils (PAO): Can be described as 'synthetic mineral oils' because of their identical structure to traditional mineral oils, the only difference being that they are manufactured from monomers such as ethylene. PAO oils can be used in refrigeration systems working in extreme conditions that are beyond the capabilities of many conventional mineral oils, thanks to their low pour points and excellent chemical and thermal stability. They have low miscibility with refrigerants and are compatible for use with carbon dioxide and ammonia. PAO oils are fully miscible with most conventional mineral refrigeration oils, but it should be noted any mixture of oils may detract from the performance properties of the PAO.
Summary
As an industry, we can help to improve energy efficiency with careful thought and planning on new equipment and employ some good practises relating to service and maintenance. It is our responsibility as individuals and as a collective industry to ensure we act in line with the legislation and take actions that support the movement towards improving energy efficiency.
Here at Climalife we have a wide range of refrigeration oils available from all the major brands and can offer a range of packaging size options. We can help advise you on the suitability of an oil to meet your system requirements.