Non-retail commercial refrigeration: Looking at the options available
Climalife UK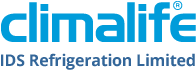
Over the next few years the F-Gas tonnes CO2 equivalents (tCO2e) phasedown should strongly encourage the use of low GWP refrigerant options. When choosing a refrigerant, it is important to note that it will be very difficult to retrofit a system designed to use a high or moderate GWP A1 refrigerant to a very low GWP A2L or A3 safety class refrigerant. This means if the refrigerant of choice for a system installed today is not low GWP and comes under pressure due to the F-Gas tCO2e phasedown, within the next 10 years there is a real risk the equipment will have to be replaced with a system designed for a low GWP alternative. It has been quoted many times by various organisations that the average refrigerant GWP by 2030 will need to be around 400 and by 2036 around 300.
In new equipment, use of any refrigerant with a GWP significantly higher than these average values should be considered as at risk of not fulfilling the expected or desired lifetime of the equipment. Our industry has always been used to retrofit options being available to prolong equipment life but this ‘escape road’ looks like it is now closed.
Using theoretical cycle calculations and considering what current standards and regulations apply, we can explore how different low GWP options compare and what is required for compliance with those standards and regulations.
Single compressor or non-retail commercial, remote condensing unit systems
Under the F-Gas regulation (2014), since 2020 it has been forbidden to install new stationary refrigeration equipment (for a product temperature > -50°C) using a refrigerant with a GWP of 2500 or higher if the refrigerant charge size is 40 tonnes CO2 equivalents (tCO2e) or higher (e.g. 10.2kg of R-404A).
This application is covered by the EN 378 standard. Within this standard is guidance on the maximum refrigerant charge that can be safely used and applies to all refrigerants, even non-flammable A1 refrigerants (Figure 1).
Within EN378 refrigerants are treated differently depending on their safety classification with refrigerant charges increasing as the risk decreases. Whilst the maximum refrigerant charges for A2Ls are lower than for non-flammable HFC refrigerants they are still significantly higher than the highly flammable A3 refrigerants (Figure 2).
As can be seen in figure 2, in this type of application, relatively large maximum charge sizes up to a charge size of 84kg can be used. This opens up the opportunity to consider A2L refrigerants for many applications where a remote condensing unit is used and the compliant charge sizes for A3 refrigerants are insufficient.
There are three options with a GWP below 300 that are good candidates to replace R-404A, namely R‑454A (238 GWP), R‑454C (148 GWP) and R-455A (148 GWP). Theoretical cycle calculations for all these options compared to R-404A giving the relative capacities and coefficient of performance (C.O.P.s) are shown in figures 3 and 4.
Another low GWP option that might be considered is of course carbon dioxide (R-744). R-744 has the advantage of being safety class A1 but still has charge limitations (figure 1) and also typically has low C.O.P. Applying theoretical cycle calculations, with compressor efficiencies based on OEM data, we can consider a hypothetical application that delivers 10 kW MT and 4kW LT refrigeration at a 32°C ambient design condition, a R-744 booster system is compared to two individual refrigeration systems (MT & LT) using R‑454C at the design condition (figure 5) and at a more typical operating condition of 15°C ambient temperature (figure 6).
DT for transcritical =2K, DT for subcritical =10K, evaporator superheat =5K, suction line superheat= 8K, compressor isentropic efficiencies - R-744 MT=68%, LT=48% - R-454A/R454C/R-455A MT=68%, LT= 67%, R-454A/R454C/R-455A liquid subcooling = 2K.
As can be seen, the differences in C.O.P. and therefore energy consumption are not trivial, leading to higher operating costs and higher total system emissions (which include emissions from power generation) when using R-744 compared to systems operating with the low GWP A2L options. Selecting a technology that has high total emissions completely undermines the whole point of using a low GWP option and this example highlights the importance of considering all the sources of emissions before selecting a low emissions technology.
Another regulatory consideration for this type of application is the Pressure Equipment Safety Regulation (PE(S)R) which is the UK legal requirement of the Pressure Equipment Directive (PED). Under PE(S)R the low GWP A2L refrigerants (except R-1234ze) fall into Fluid Group 1 which, compared to A1 refrigerants, lowers the threshold levels where more stringent safety requirements are needed.
For example, consider a system with a 3-litre liquid receiver on the high pressure side:
If this system was operating with R-404A, R-448A or R-449A, which are fluid group 2, then it would be PE(S)R Cat I which can be self-certified by the manufacturer without notified body involvement using industry standard brazing qualifications.
If a similar system was designed to use an A2L refrigerant such as R-454A, R-454C, R-455A (fluid group 1) or high pressure R-744 (fluid group 2) then this would be PED category II requiring notified body approval for brazing, system certification, quality assurance procedures for production and pressure testing with witnessing of some system pressure tests also required. These increased requirements when changing from moderate pressure A1 refrigerants to either flammable or high-pressure A1 refrigerants are the main reasons why it would not be practical to retrofit existing equipment to these products in the field.
When designing systems with A2L refrigerants it is advisable to minimise the refrigerant charge by minimising the size of liquid receivers and considering the use of microchannel condensers. This will minimise the risk and environmental impact, maximise the opportunities and reduce the regulatory requirements.
The time for change is now!
Whilst availability of moderate to high GWP refrigerants is still good, it is easy to be lulled into the false sense of security that the time to change is somewhere in the future, but already systems being installed today run a very high risk of not fulfilling their expected lifetime due to the choice of an unsustainable refrigerant.
Low GWP refrigerants are readily available, and the availability of suitable equipment is rapidly increasing meaning there is no reason why a sustainable low GWP can’t be installed today. In many cases improved energy efficiency can be achieved using A2L refrigerants lowering operating costs as well as reducing emissions for the expected lifetime of the equipment.
It is human nature to try to avoid change but this one is inevitable so while there is still time, why not get ahead of the legislative curve and steal a march on your competition?