Future proofing eco-friendly portable cold storage and blast chiller/freezer units with low GWP R-454A (Opteon™ XL40)
Climalife UK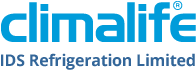
Innovative Refrigeration Solutions from Ultra Refrigeration Ltd
Derbyshire-based Ultra Refrigeration Ltd is at the forefront of commercial refrigeration solutions, designing, building, and installing blast chillers/freezers and cold storage units for the food and drink, storage and distribution, pharmaceuticals, and manufacturing sectors. The company is committed to delivering innovative, technology-led, sustainable, and energy-efficient products to its customers.
Seeking Cost and Energy Efficiencies Without Compromising Reliability
Working with a producer of portable, blast chillers/freezers and cold stores that had historically used R-449A (GWP 1397), Ultra were looking to test a lower GWP refrigerant to reduce the environmental footprint of their new units, without compromising on the system performance.
Already in regular discussion, Climalife’s Technical Sales Director, Neil Roberts and Ultra Refrigeration’s Operations Director, Anthony Lomas considered the various refrigerant options available for the new unit designs taking into account predicted performance, product availability, safety and environmental credentials.
Several refrigerants were assessed, including CO₂ and options with a GWP below 150, but due to blast freezer capacity requirements and the need for easy transportation, Opteon™ XL40 | R-454A (GWP 239) emerged as the most suitable solution.
It’s worth noting that the lowest GWP refrigerant isn’t always the best solution for a project. The location, cost, energy efficiency and reliability should all be considered too which is why it’s key to seek out the expert advice of companies like Climalife when specifying a new system.
Neil Roberts commented “Uncertainty around the changes in legislation often leads to a delay in taking decisions, so it’s great to be able to assist a manufacturer and end user with the foresight to get ahead of the imminent legislation changes by moving to a very low GWP, sustainable and energy efficient refrigerant option and potentially setting a new benchmark for others in the industry to follow.”
Ultra were very keen to future proof their equipment for the next 10-20 years at least and so commissioned a trial with their blast freezers using Opteon™ XL40 | R-454A in August 2023, alongside an identical unit running under the same conditions, containing R-449A.
Trialing R-454A in Cold Storage and Blast Freezing Applications
From left to right: R-449A blast freezer, R-454A cold store, R-454A test blast freezer
Cold Stores
The cold store unit performed smoothly during testing, with some system adjustments made to accommodate pressure variations. Following successful trials, the unit is now in full production, with the first delivery to a client’s site completed in July 2024.
Blast chillers/freezers
The blast freezer trials revealed key differences in refrigerant performance. Initially, the R-454A unit did not operate as efficiently as the R-449A unit. Due to slight differences in pressure/temperature relationships, the existing control system—originally designed for R-449A—was self-limiting performance unnecessarily.
To address this, Ultra Refrigeration optimised the control system, allowing the R-454A unit to perform at a comparable level of efficiency to its R-449A counterpart with all of the environmental benefits.
During the testing phase, IBCs full of water were stored in the blast freezers to simulate product load.
Pressure Equipment (Safety) Regulation
Any system with a pressure over 0.5 bar must comply with the Pressure Equipment (Safety) Regulation (PE(S)R). Systems are categorised from SEP (Sound Engineering Practice) to Category 4, based on factors such as system volume, pipe size, fluid risk category, and pressure.
- The R-449A system was classified as Category 1, using an A1 refrigerant (fluid group 2).
- The R-454A system fell under Category 2, using an A2L refrigerant (fluid group 1).
This change in classification required additional safety compliance measures, new component sourcing, and the involvement of a notified body to certify the system. Updates to welding, brazing certifications, and software were also necessary.
Anthony Lomas stated, “Despite an initial steep learning curve and some additional costs, once the required changes were made, manufacturing the system was relatively straight forward and not significantly more complex than the previous design.”
Blast freezer