Energy efficiency, good for your pockets as well as the environment
Climalife UK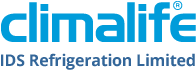
This time last year, energy efficiency was seen as more of an emissions mitigation strategy, with benefits, to help to stave off the impacts of global climate change. Fast forward a year and now energy efficiency is a critical tool to keep down operating costs.
It has always been known that refrigeration and air conditioning are large consumers of energy so even modest gains in energy efficiency can deliver significant savings over the lifetime of the equipment. System design and refrigerant choice are major considerations, but there are other actions that can be taken to maintain or improve energy efficiency, reduce total emissions and in most cases, they will even pay for themselves over the lifetime of the equipment.
Good Maintenance and Correct Control Settings
This is probably the easiest strategy to employ but often end users do not see the benefits of spending money on a system that appears to have nothing wrong with it. Simply cleaning the heat exchangers, using reliable gas detection methods, ensuring fans are operating correctly and optimising the system operating parameters can have a significant impact on system emissions.
Even moderate fouling of a condenser will lead to an increase in condensing temperature of the system. Equally if the system has a high/condenser pressure controller, checking the setting is not causing the system to operate at excessively high conditions or is set correctly for the refrigerant used (for example after a retrofit) can have a big impact.
Figure 1-Degradation of C.O.P. with increasing condensing temperature for R-449A
Figure 1 shows the impact of increasing condensing temperatures with R-449A at low and medium temperature conditions. Even a very small increase in the condensing temperature can lead to significant decreases in energy efficiency, for example, an increase from 25°C to 27°C condensing temperature can lead to a 5-8% loss of compressor energy efficiency.
Pressure increase caused by condenser fouling is easily prevented by regular use of cleaning products such as Frionett® condenser coil cleaner which will prevent build-up of debris that can block the air flow through the coils, maintaining the optimum energy efficiency.
In situations where condenser fans have either failed or are malfunctioning, energy efficiencies could easily drop by 25% or more.
Table 1 - Pressure differences of R-404A alternatives
Systems which have been retrofitted and have high pressure controllers can often lose some of the energy efficiency benefits available if the controllers are not correctly adjusted. For example, if a R‑404A system is retrofitted to a lower GWP alternative, it is very likely the alternative product has a lower pressure temperature relationship (Table 1). If the pressure controller is not lowered to match the new refrigerant, then the energy efficiency of the system could be 5-10% lower than for the optimum setting.
Refrigerant choice
Different refrigerants do have different energy efficiencies when used in the same equipment. In practice there are many potential variables that can affect this, but if it’s thermodynamically proven then it should be possible to achieve improved energy efficiency if the system is set up correctly. Equally using the same refrigerant in both medium temperature and low temperature applications, whilst convenient, may not deliver the highest achievable energy efficiency and its high time this practice is addressed.
Table 2 - Theoretical cycle calculation comparisons
For example, using theoretical cycle calculations for medium (-8°C mean, MT) and low temperature (-35°C mean, LT) refrigeration conditions* it can be seen in table 2 that all the lower GWP like for like alternatives for R-404A have a higher energy efficiency. It can also be clearly seen in table 2 that using two different refrigerants in the MT and LT systems has the potential to significantly increase the energy efficiency even further.
Technology choice
Choosing a refrigerant with low GWP does not necessarily mean good energy efficiency. Due to a F-Gas regulation ban which came into force in 2022, R‑744 (GWP=1) has become a common choice for retail refrigeration systems of 40kW or larger cooling capacity, however, there is a growing body of evidence that shows the use of R-744 may not be the best choice for energy efficiency. A recent case study published by Chemours has presented results supplied by the retailer Asda from a store using several R-744 booster systems but has now been changed to modular systems using R-454A as the refrigerant. Using energy monitoring of the refrigeration systems before and after the change of technology, Asda reported a reduction in annual energy usage of 34% when using R-454A compared to the previous R-744 system.
Similarly, the dominance of ammonia in industrial refrigeration is also being challenged. In a case study from Climalife, Optinenergie (a French engineering company specialising in industrial energy performance) reported that in a medium temperature fruit store, a R‑1234ze chiller installed in 2020 can achieve up to 25% higher C.O.P. values than an equivalent ammonia installation that was installed in 2015 at the same site.
It is very clear from these recent studies, and several previous reports, that technology choice is a major factor in achieving the most energy efficient solution available.
Heat Recovery
This is a hugely underutilised technique which has the potential to greatly reduce energy usage by re-using the waste heat produced from the refrigeration system, or indeed any process that produces excess heat, that in the past has been expelled to the environment.
Figure 2 - Results of a heat recovery study using R-454C and R-744
A white paper published by Chemours in July 2021 considered heat recovery from a supermarket of approximately 2300m² sales floor area using either R-454C or R-744 and compared the results to a basic R‑404A refrigeration system with either a gas boiler or air source heat pump (AS HP) for all the heating requirements. The results considering numerous heat recovery strategies for a typical UK climate (Leicester) are shown in figure 2 and demonstrate the huge potential for lowering total system emissions, the majority of which are achieved by reducing energy consumption.
It is very clear from the results of this study that heat recovery will greatly decrease the energy consumption with any refrigerant and easily justifies the higher initial installation cost.
In summary
With governments setting targets for reduced emissions and energy usage, it is clear the refrigeration industry has an important role to play. To achieve the maximum reductions available, it is important to thoroughly investigate all the options and not just make decisions on a single parameter, such as refrigerant GWP. As shown in this article, low GWP does not necessarily mean high energy efficiency and a poor choice of refrigerant technology may even lead to an increase energy usage, operating cost and total lifetime emissions. Advice on which solutions best fit your requirements is readily available and the team at Climalife have the tools and knowledge to lead you to an eco-efficient future.
*Theoretical calculations made for a 4kW LT, 10kW MT cooling load, with 2 individual systems. Superheat (13K, 5K useful), subcool (2K), mean condensing temperature 25°C and compressor efficiency (0.65 MT and 0.64 LT) values were the same for all refrigerants.